20 November,2020
Hi,
To move the main hull out of the shed and complete the floats the main hull needs to be laid over on a trolley so it can pass through a 3 metre wide opening. I have built the trolley
using 75x75x3 square hollow section steel on large castor wheels strong enough to handle the weight.
To get the hull onto the trolley I have built 2 Gantry cranes from 75x75x3 square hollow section steel with the uprights welded to the floor bearers and the top beam bolted to the
uprights. Fran helped stand the frames up and a chain block attached to each beam. I purchased polyester slings from a specialist lifting shop and set them up one about station 3 and
one about station 8.
We selected a day when all our bones and muscles were aligned and Fran and I lifted the hull onto the trolley. After 6 months of stress and anxiety and many coffees it was all over in
about an hour. Now to lay the hull over and move outside.
The floats which are on their own trolleys will be moved inside and the beams attached and the whole assembly painted, moved outside and mounted to the main hull.
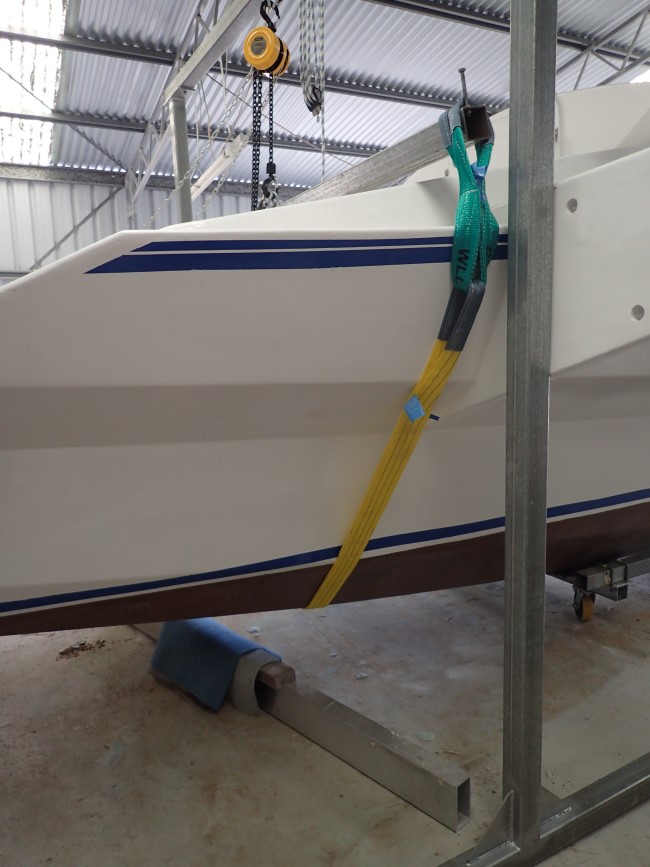
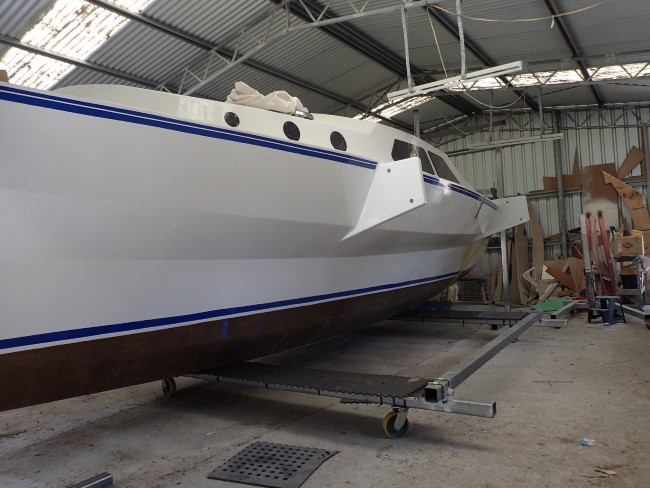
|
1 October, 2020
Hi,
Since the last entry I have coated the deck and cockpit with Kiwi Grip non skid deck paint. Bolted the anchor roller and mooring pennant roller to the deck. Painted the stripes,
one just below the gunwhale and one just above the antifouling as a boot topping.
The Kiwi Grip non skid went on well. First off masking tape was used to mask around hatches and where fittings will be located, eg winches, cleats and mast steps. The masking is
a big job, quite time consuming. The Kiwi Grip is applied with a thick brush and then textured with the special texturing roller. The finish can be modified for the depth and
severity of the non skid by adjusting the pressure on the texturing roller.
We have used other non skid applications, powdered glass on paint, non skid straight out of the can and rolled on etc but the Kiwi Grip has been the easiest to use so far.
The anchor and mooring pennant rollers are from EX-CELL same as the anchors, they are a bit expensive but beautifully made, real works of art. I hade to make two L shaped brackets
to bolt to the sides of the stem to effectually extend the deck so that the mounting was efficient with enough bolts holding it horizontal.
The stripes were painted on using a brush and Jotun Imperite gloss paint. The masking was a big problem as most masking tape is only good for use as sticky tape for wrapping
sausages or similar. The best one I found was PHP tape from the chandlers, I cannot find it at hardware stores. It does not seem to matter how well the other stuff is applied,
firmed down etc the paint will still find a way down, not a problem on horizontal surfaces but a problem on near vertical surfaces.
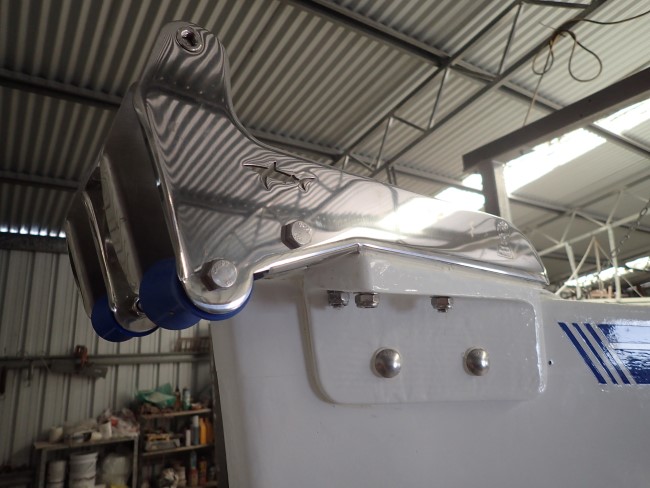
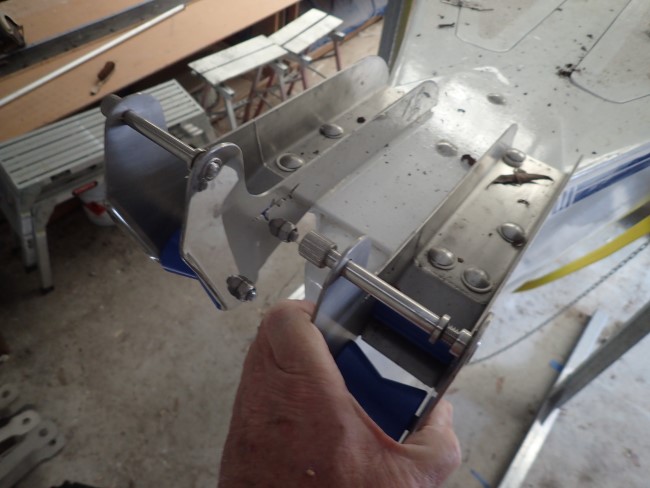 |